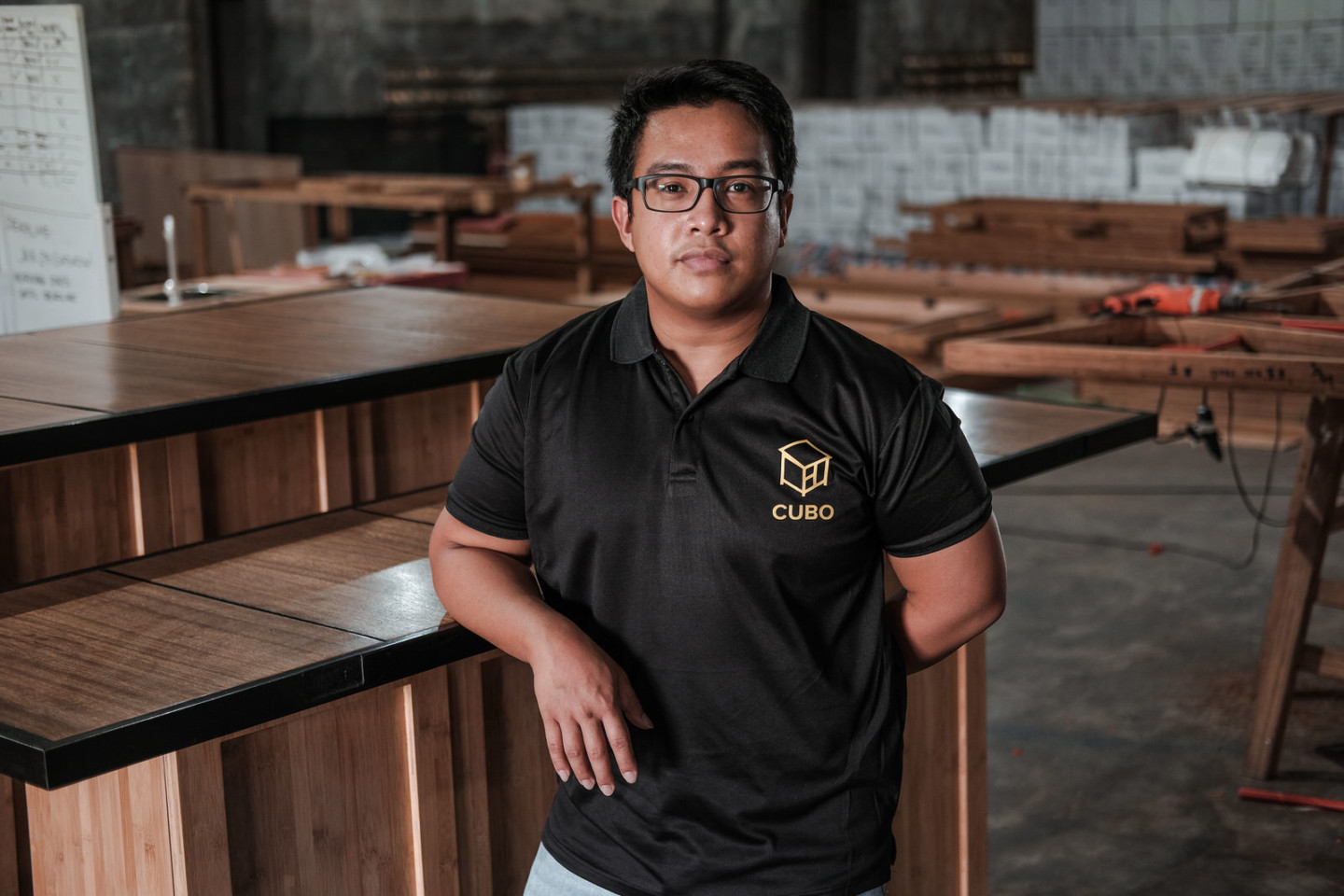
Bahay kubo is a national symbol, an icon of Philippine culture. It is a simple and traditional house that has retained its charm from pre-colonial period until now. Despite the technological advancements, it’s worth noting that these mighty houses are still common sights especially in the rural areas up to this day.
Earl Forales is one such individual who saw the value and charm in our traditional bahay kubo. With the advancement in construction technologies and the inspiration from the traditional Filipino home, it became his mission is to translate that concept into 21st century homes—equipping this icon of Philippine culture with even sturdier materials able to withstand the increasing changes in the environment. And that’s how Cubo Modular was born. Cubo Modular is a company initially founded to help solve the housing crisis in the Philippines by providing low-cost, sustainable, and dignified housing to Filipinos.
In 2018, then 23-year old Earl Forlales and his business partner Zahra Zanjani topped the Cities For Our Future Challenge, an online global competition by Royal Insitution of Chartered Surveyors (RICS) for transformative ideas solving issues such as rapid urbanization, climate change, and resource scarcity. “I submitted the idea of upgrading a traditional bahay kubo, and we won that competition over 1,200 designers/architects around the world. They gave us a prize money for it which was great because we were able to prototype that solution right away. We won in November 2018, and by January 2019, we already had a prototype,” shared Earl. And two years after winning the competition, they have started manufacturing for different clients, with Earl Forlales taking the helm as CEO, and Zahra Zanjani as the COO.
Coming from a materials engineering background, Earl saw the potential of engineered bamboo, given that the country already has the abundant supply and the technology. Earl explained, “It was an idea that we really had to act on because we are underutilizing bamboo. DOST has the knowledge, DTI has the equipment, and they even train people how to process engineered bamboos.”
Images — Zaldine Alvaro
Cubo Modular is a truly Filipino solution—from the design, all the way to the assembly, it all goes through the crafty and resourceful hands of Filipinos. They currently have three standard models aptly named: the Batanes, Bulacan, and Sarangani. The Batanes, being their most compact model is 6.5 sqm, but can be equipped with a bathroom, kitchen, and a loft. The origin model base package starts at only P89,000. “What we’re trying to bring into the market also is the idea of the tiny house movement. The bahay kubo is essentially a tiny house, at the same time it’s also very modular. We just have to upgrade the material, put it in a 21st century setting, and manufacture it so we can scale it,” Earl said.
What surprised Earl Forlales and the Cubo team is that the idea of owning a home for as low as P89,000 did not only catch the attention of home buyers, but also those in the hospitality industry. Now, their clients range from the mass sector to resort developers, and they have also deployed some units as isolation homes or quarantine facilities, as a way to respond to the current global crisis. Earl added, “That’s P89,000 worth of housing that even resort developers want a piece of. So that for us checks the dignified part. You know, you can get a P89,000 house but you won’t put it in a resort. The solution offering is something presentable that even hospitality and mass sector would be interested in.”
Despite being low-cost, Cubo is committed to deliver quality homes, following the International Residential Code (IRC), ensuring that the product is typhoon-proof and earthquake-proof, especially for a disaster-prone city like Metro Manila. As a proof of this concept, the day after they delivered the first unit in Mandaluyong, a magnitude 6.3 earthquake struck Metro Manila, and the unit stood still, without any damage.
Aside from the superior mechanical properties of engineered bamboo, another interesting fact is that bamboo is a plant that harvests carbon dioxide. Earl shared, “in every 1,000kg or 1 ton of bamboo that you plant, it harvests 600kg of carbon dioxide in the atmosphere. And it’s unique because if you scale that solution, they essentially have a carbon-cleaning material that you can turn into homes.”
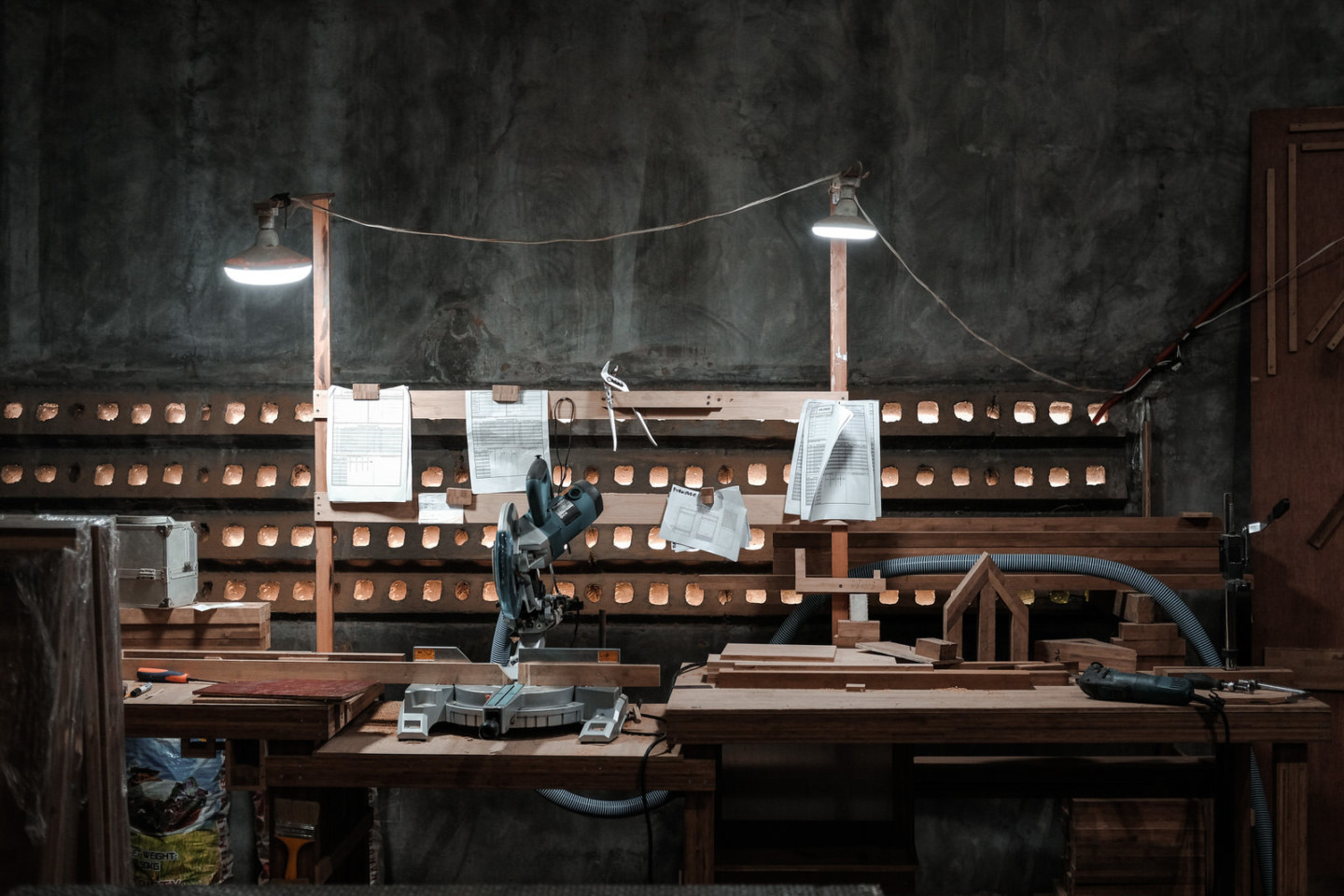
Traditional construction materials such as iron, steel, and concrete, are identified as carbon emitters, and the consumption of raw materials by the construction industries is one of the causes of the depletion of natural resources. This is the reason why Cubo is keeping their pledge to do their part in protecting the environment. “For us, it didn’t make sense to use concrete anymore. The real problem is global warming. 7% of the global carbon emissions are coming from cement or concrete only. That’s why we believe that engineered bamboo is the future,” said Earl.
For Earl and his team, it’s really the need that brought out the solution. “A need for a sustainable housing solution, and the need for a low-cost home that is dignified. You can either find dignified and sustainable solution, but it won’t be affordable. Or dignified and affordable, but not sustainable. You’ve probably found sustainable and low-cost options, but they don’t look good either. It’s really the combination of those three that make the best solution in our opinion,” said Earl.
Now more than ever, more people are being aware of the concept of sustainability, and Cubo is overwhelmed with how the market responded to their innovation, getting hundreds of e-mail inquiries in their social media messages and comments. Earl mentioned, “We are definitely overwhelmed, but it’s also a realization for us that there is indeed a demand for this type of housing solution, that we need to scale up as much as possible, so we can deliver to more people. But we’re also taking it very slowly because we also don’t want to bite more than we can chew because we know we would be sacrificing quality at the end of the day if we do that.” Production backlogs aside, one unit of the Batanes model will only take one week to manufacture in their warehouse, and 4 hours to assemble in the chosen location of the unit owner.
Being in the business for only half a year, Cubo has a lot of things they can look forward to. As a company, they are looking at partnering with the government agencies, thinking of ways to integrate the solution to the government projects because they believe that it is where mass scale can come in.
“We have 4 million families who do not have a home to go to at the end of the day. So we’ve made it our mission as a company to provide Filipinos with that option—having a dignified, sustainable home, without destroying the environment,” Earl added. In terms of expansion, Earl and his team are seeing it in two ways—a possibility to construct an all-bamboo building since there’s already a technology at hand, and the development of Cubo communities. “Imagine having a resort-type, low-cost housing development, all bamboo, multiple kubos. It’s essentially like being living on a vacation,” Earl smiled, as he shared his goals for the company.
Cubo is truly establishing themselves to be a very promising brand, and the now 25-year-old Earl Forlales is more determined to succeed in their mission to deliver the solution that they promised and take pride of—a low-cost, dignified, and sustainable home for Filipinos.
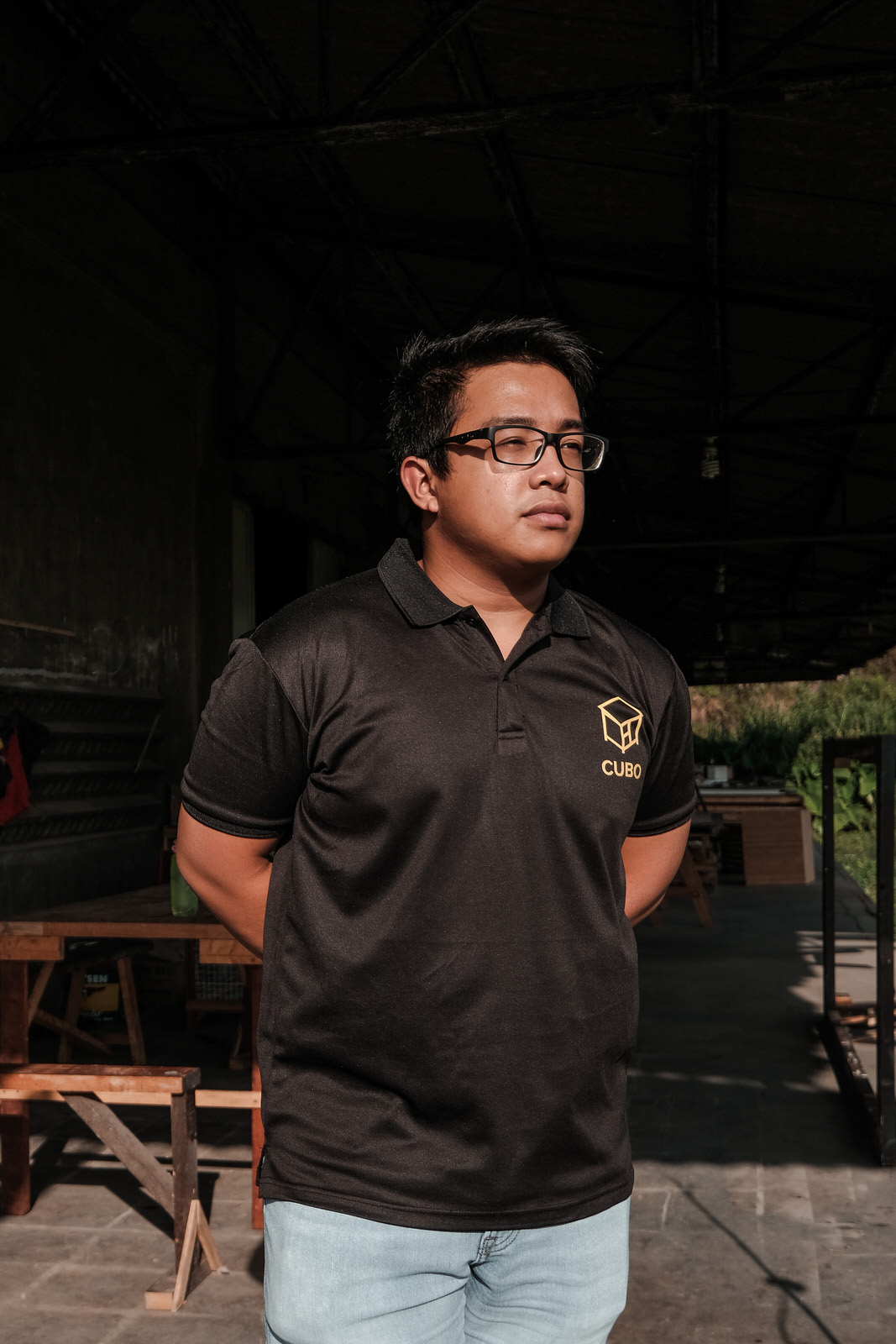